|
|
|
|
|
|
|
|
|
|
|
|
|
AIR BLASTER |
|
|
|
|
|
|
|
|
|
|
|
|
|
|
|
The basic principle of Baani Air
Blasters operation envisages introduction of Compressed air at a
velocity with kinetically activates dust particles clinging to
any surface, with this enrgery making them vibrate and break
free from other particles and surface to with they had adhered.
The compressed air is stored in an
air receiver which maintains the air pressure at 6 to 7 kgf/sq.
cm. This compressed air is fed to the point of discharge through
a 100 mm. |
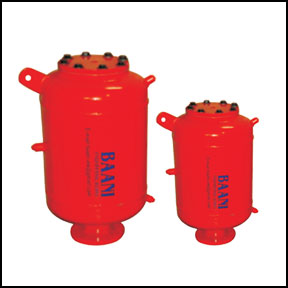 |
|
|
|
|
|
|
|
|
Opening through operation of pneumatically controlled valves.
The sudden but controlled release of compressed air into the
stored material is at a rate faster than the material can absorb
it, thereby causing the material to get dislodged and move. The
controlled release of air ensures that the reaction is not
transmitted to the support structure and also there is minimal
effect of noise or vibration. The actuation of the blaster can
be effected either manually or through Electronic Sequence
Timer. |
|
|
|
|
AIR BLASTER WITH ALL
STANDARD ACCESSORIES |
|
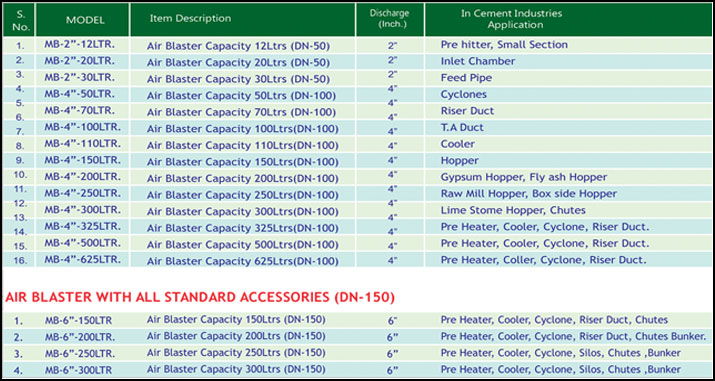 |
|
|
|
|
|
|
One Cycle of filling and release is
described as follows : Fillings : Compressed air is
supplied through air pipeline controlled by a solenoid valve to
quick exhaust valve. The diaphragm of quick exhaust valve closes
the 3/4 inch outlet. The compressed air flows past the diaphragm
into the piston chamber. The compressed air flows past through
an opening in the piston into the receiver and fill it with air
untill the pressure in it equals that in the pipeline. The
pressure in the receiver is maintained and the unit is now READY
OR FIRING.
Release : By actuating the
solenoid valve, bothe and control air in pipeline and the
compressed air stored up behind the piston are released by
simultaneous actuation of the quick exhaust valve. The
compressed air stored inside the receiver makes the piston to
lift off its seat and after moving equal to only a quarter of
the outlet pipe diameter release the whole discharge cross
section without restriction loss. The air is blown very rapidly
within milliseconds into the Bunker, Hopper, Silo, Chutes etc.
So that an almost explosive effect is obtained. After this, the
spring forces the piston back to its initial position so that
the outlet is closed again and no material can get into the
interior of the vessel.
Firing sequence is from bottom to top in case of Hopper,
Bunkers, Chutes and Cyclones and the sequence is from top to
bottom in case of cement pre-heater tower. |
|
|
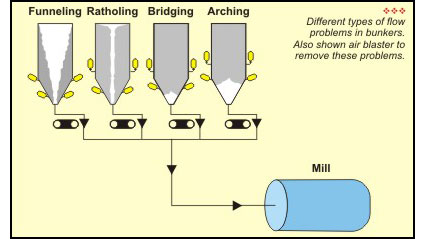 |
The Advantages :
The Baani Air Blasters offer several advantages coupled with
diversity of their use or various industries which assume
importance in view of greater necessity of uninterrupted plant
operation.
Cleaning without interruption of production.
Cleaning without Damaging.
Cleaning improves plant efficiency.
Lower Service and Maintenance cost. |
|
|
|
|
|
|
Applications : Some Installation in Cement Plant |
|
|
|
|
|
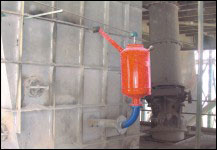 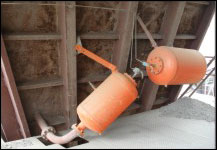 |
|
|
Air Blaster Installed for removing
Coating in Grate Cooler. |
Air Blaster Installed for removing
Coating in Pre-Heater Chamber (Duct). |
|
|
|
|
|
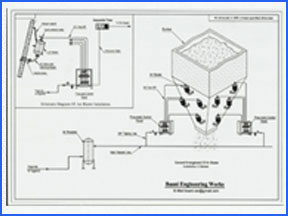 |
|
|
Large Image |
|
|
|
|